Brick production has been done in the same way all over the world for centuries. Briefly, we could say that this process involved soiling, molding, drying, and finally, creating bricks. Factors such as the London Fire of 1666 and the Industrial Revolution made people recognize brick as a refractory and fire-resistant material. Hence, the consumption of brick became more popular. But today, we use the most modern equipment and fully automatic brick production machines and produce bricks by European standards. On the other hand, we use shale raw materials to respect and preserve the environment, which is the most significant duty of all humans.
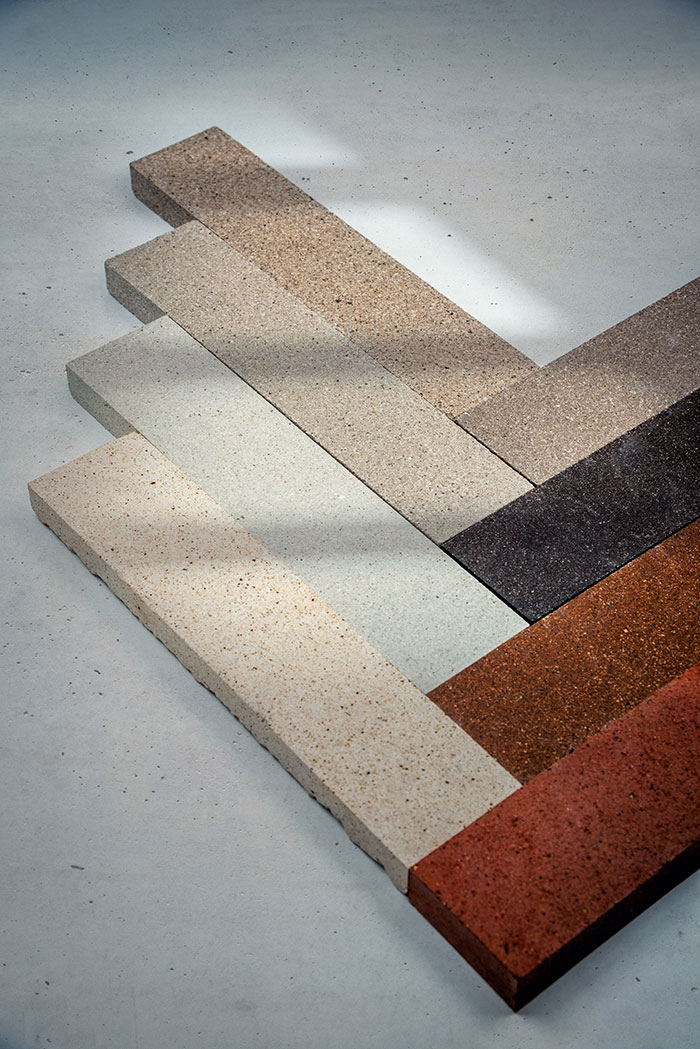
At present, SBCD member of a brick home company with the benefit of European brands of experienced workers and experts with their professional use of modern European technical knowledge and machines, as well as obtaining quality and management standards, is expanding its share in regional and world markets for its manufactured products.
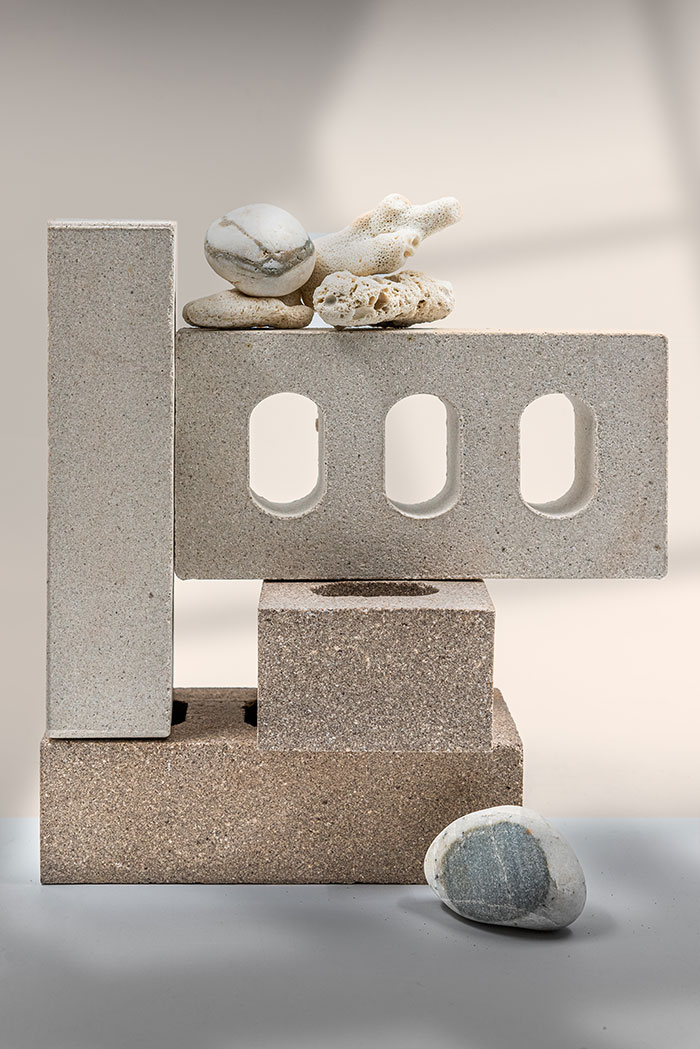
The smooth Executive of the brick depends on the degree of convexity or concavity of the bricks. Still, bricks must go through the phase of grinding and fusion, so they may sometimes be a little complicated and uneven, but the standard is acceptable for high-quality bricks; it defines that one millimeter of convexity and two millimeters of concavity is allowed, but the bricks which they are less than this or have been produced perfectly smooth, will be in the highest quality.
Tolerance and dimensional differences in first-class brickwork affect the performance and design. When we calibrate the bricks, the clauses of the bricks will be regular and matched, so in a first-class brick, the difference in dimensions will be so low. According to the national standard, the maximum tolerance for a first-class facing brick, with a size of 25 to 35 cm, should not be more than 6 mm, meaning it should be about 3 mm on average. Therefore, the lower the dimension difference, the higher the quality of the brick from this perspective.
The porosity of the brick causes it to absorb water and moisture. The higher the porosity, the higher the water absorption. Absorption of high water causes the bricks to freeze and crumble in the face of extreme weather changes. Absorption of first-class brick water, according to the national standard, should be less than 18% and more than 6%
One of the quality indicators of bricks is their bending strength. Those bricks that are out of standard do not withstand the stresses that enter them, so they break down quickly. According to the national standard, thin bricks’ minimum average flexural strength should not be less than 40 km/cm.
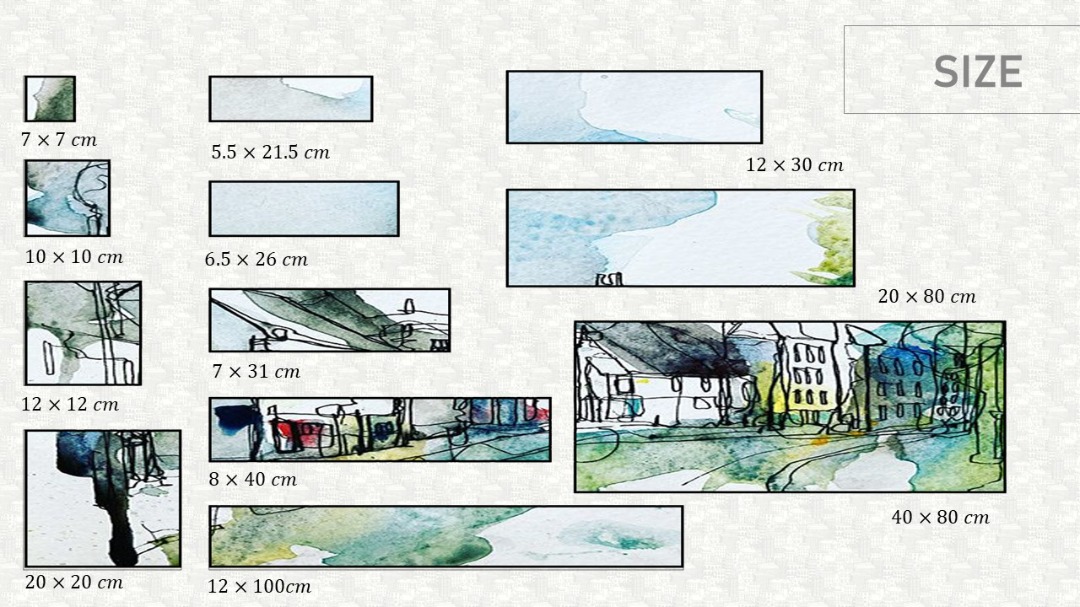
the amount of pressure tolerance applied to the brick is called compressive strength. Compressive and bending strength are usually directly related, indicating the product’s resistance to building stresses or external forces on the brick. It is better than the average minimum compressive strength on first-class facade bricks, be 140 km/cm. Bricks with this feature usually had problems during production, poor-quality materials, or had not been completely baked.
Energy saving and moving forward to green buildings are a “must do” nowadays, and the materials used in the surrounding walls will be affected by factors. The lower the thermal conductivity of the material, the higher the thermal resistance and the lower the energy loss. Thermal resistance is calculated based on the formula R=L/H, in which the variable R is the thermal resistance itself, L is the thickness of the material in use, and H is the thermal conductivity. The heat transfer coefficient of brick is from 6 percent to ½, limestone is about 1/3, and siliceous rocks are from 2 to 7. O
According to the lack of knowledge about the raw materials in the past, this kind of clay had been popular in Europe for centuries ago, and although in some cases, the product of this clay met the standards, nowadays, because of the environment and due to reduced sources, using this type of material will be very di “cult. It’s a type of sedimentary rock from the sedimentation of fine-grained soils. Shales have a layered shape, typically composed of quartz grains, carbonate alkaline earth oxide, and clay minerals, and clay is one of their most essential combinations. The color of shales is usually grey, but depending on the components of the rock, they can be red, brown, yellow, or green. Shale classification based on their minerals is as follows: petroleum shales, feldspar Shales, mica shales, and siliceous shales.
There is an important note about shales: shales give the producers a huge color diversity, and they make bricks with higher compressive strength and bending strength. In addition to this great advantage, we should mention that the manufacturers can produce in even larger dimensions. One of the major problems of the dimensional brick industry is that some factors such as grain size, soil type, the drying process, and the type of furnace are influential in it, and shales are a great answer to reduce them. Still, even more, critical is the drying process.
Because the raw material for making bricks was clay, this over perception caused many problems and became an ecological problem. An alternative material to solve this problem was shales; shales are minerals that, due to having unique materials after being crushed and turning into tiny pieces, are suitable for making bricks and follow precisely the same path of producing bricks from clay.
Our factory group has been able to design and manufacture modern dryers that blow hot air at a controlled temperature between the brick biscuits to minimize the impact of the drying stage of the bricks on dimensional tolerances. This group of factories, using the most modern ovens in the world designed by Italian companies, perform the baking process with the latest method in the world so that we can see the best quality in the products.